SERVICE
S
寧波美仕高潔塗料有限公司是一家大型塗料生產企業(yè)
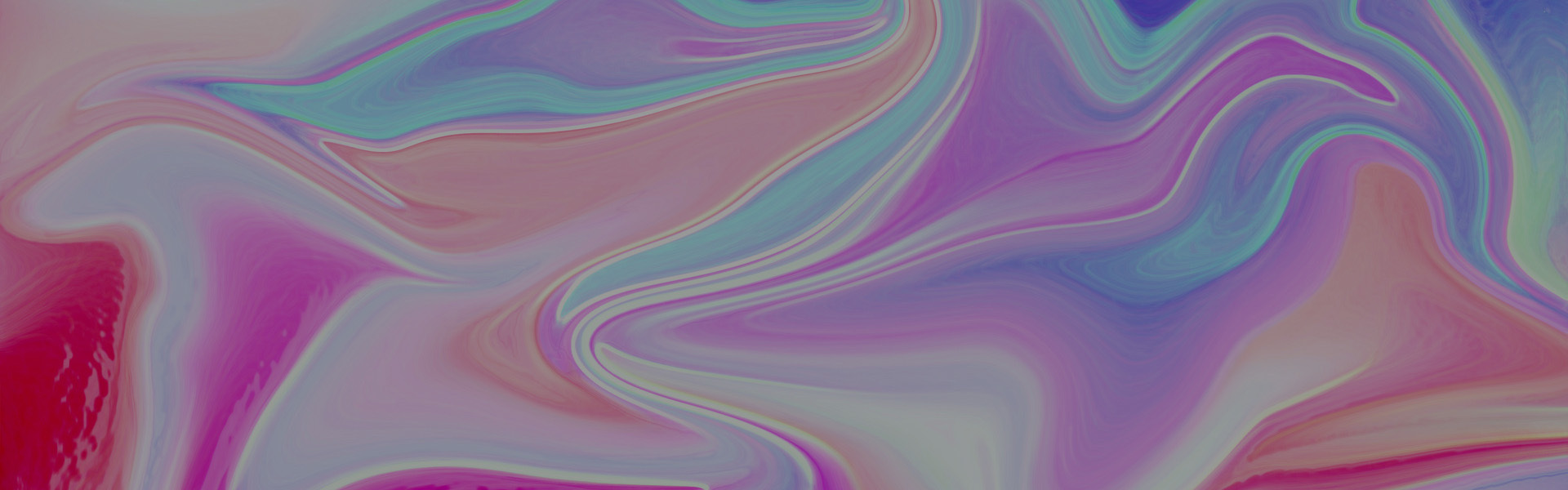
成因
(1)涂料粘度過高,或涂料用合成樹脂的分子量大,按普通施工粘度時出現(xiàn)拉絲;
(2)稀釋劑的溶解力不足或揮發(fā)速度過快;
(3)噴涂施工時霧化過度,噴嘴太小或操作失誤。
改善對策
(1)按說明書要求調整漆料的粘度,也可加入適量的高沸點溶劑;
(2)選擇溶解力強的溶劑,高溫環(huán)境中施工時,更應注意溶劑的選用;
(3)降低噴涂壓力,縮短噴距,采用大口徑的噴槍。
成因
(1)流涂和浸涂施工中,涂料會在物件的邊緣和底部堆積、變厚;
(2)烘烤型漆在干燥過程中由于邊緣處的溶劑揮發(fā)較快,涂料中基料的表面張力比溶劑高,出現(xiàn)的表面張力梯度,使涂料流向底材的邊緣處。
改善對策
(1)調整漆液適宜的粘度,多層薄涂;對裝飾性要求不高的情況下,可直接進行下道的涂裝;對高裝飾性的漆膜,應將厚邊部分除去,打磨后再進行補涂;
(2)加入適量的表面活性劑以改善漆膜的表面張力;
成因
(1)干燥快的油漆與干燥慢的油漆攙和使用,兩層漆膜干燥的速度不同,導致皺紋;或漆膜未完全干燥時在其上覆涂下一道漆膜。
(2)表干速度過快而實干慢之漆料粘度過大,漆膜過厚,超出常規(guī);
改善對策
(1)保證漆膜完全干燥后,方進行下道漆的涂裝;減小涂料粘度,降低漆膜厚度;
(2)調整合適的干燥速度和粘度;對于起皺嚴重的漆膜,應鏟去重涂;對于輕微的起皺,可用細砂紙打磨后,再次涂裝。
成因
(1)涂料中顏料含量過低或遮蓋力太差,或使用了透明性顏料;
(2)涂料混合攪拌不均勻,有沉淀未攪起;
(3)涂料的粘度過稀或加入了過量的溶劑;
(4)漆膜太薄或噴涂時走槍不勻,有漏涂現(xiàn)象。
改善對策
(1)提高顏料遮蓋力;
(2)油漆在應用前應充分攪拌均勻,不應有沉淀存在;
(3)按規(guī)定調整漆液的粘度,不要加入過量的溶劑;
(4)規(guī)范施工,防止漏涂,噴涂時注意走槍速度,覆涂邊緣占槍幅的1/3;對于輕微露底者,可用毛筆或漆刷蘸取該色漆補勻;出現(xiàn)較普遍的星星點點的露底時,用細砂紙將漆膜打毛,除去灰塵后, 重新涂裝;對于不能蓋住底色的,應再噴涂一道面漆。
成因
(1)兩種以上色漆相互混合不充分;顏料的密度相差懸殊,密度大的沉底,輕的浮在上面,攪拌不徹底以致色漆有深有淺;
(2)涂料的粘度不適當,由于對流引起顏料的波動,其中細的、密度小的向表層移動,大顆粒、密度大的難以移動,于是產生浮色或發(fā)花現(xiàn)象;濕漆膜表面受熱不均,造成表面張力差,也會產生浮色發(fā)花現(xiàn)象;
(3)溶劑過多或選擇不當,揮發(fā)速度不平衡;
(4)一次涂裝過厚,漆膜上下發(fā)生對流、發(fā)花而形成六角形的小花紋;
(5)施工容器內殘留的其它顏色的色漆未清洗干凈。
改善對策
(1)施工前,一定要將油漆攪拌均勻;
(2)適當增加涂料的粘度,減少漆膜表面的表面張力梯度;
(3)夏季施工時,選用揮發(fā)性較慢的溶劑,冬季則相反;
(4)一次涂裝不易太厚,降低漆膜厚度,多道薄涂;
(5)清洗干凈施工容器。
成因
(1)施工中,底漆未干透或涂裝含有強溶劑的面漆,使底層漆膜溶解;
(2)底層中使用了干燥極慢的材料,再進行涂裝時,易出現(xiàn)滲色;
(3)涂裝底漆前,未清除物面上的油污、染料等。
改善對策
(1)施工時,按照配套原則選擇面漆,不能用含有強溶劑的涂料作面漆;施工應有一定的時間間隔,使底漆充分干透, 噴涂不同顏色的強溶劑涂料時,應適當 減少稀釋劑的用量,同時宜薄涂;噴涂施工發(fā)生滲色時,應立即停止施工,對已噴涂的漆膜進行處理;
(2)發(fā)生滲色時,只會影響漆膜的外觀,一般不會影響漆膜的防腐保護效果;可在發(fā)生滲色的漆膜表面再涂一道面漆,也可加涂中間涂層后再涂面漆;對裝飾性要求較高的漆膜,可將滲色部分用細砂紙打磨均勻后,補涂相應的面漆。
(3)底材一定要徹底除去油污、染料等污物;
成因
(1)涂料存放時間過長變質,或涂料細度不合格;
(2)稀釋涂料時所采用的稀釋劑與涂料不匹配;
(3)涂裝場所不清潔或在風沙天氣施工,有煙塵、碎屑、風沙落在未干燥的漆膜表面;刷涂施工時,漆刷上的顆粒或砂子留在漆膜上;噴槍不潔,用過醇酸類等油性漆的噴槍噴雙組份漆時,溶劑將漆皮咬起形成殘渣混入漆中;
(4)噴涂時,噴槍距被涂物面過遠,使噴霧落在物面之前涂料中的溶劑已經揮發(fā),導致漆液失去了流動性形成顆粒;當噴涂時噴嘴口徑小、壓力大,也會造成粗顆粒的噴出。
改善對策
(1)保證涂料細度合格并在保質期內;
(2)采用與涂料相溶性好的溶劑,防止樹脂的析出;;
(3)保持施工環(huán)境的清潔,避免在大風的天氣下施工;施工工具應及時清洗,防止雜物混入;
(4)噴涂施工時調整適當?shù)膰娮炜趶胶蛪毫Γ瑖娋嗖粦h。
成因
(1)涂料中含有揮發(fā)性差的溶劑,如高沸點芳烴溶劑等;
(2)催干劑調配不當,用量不足;
(3)施工時天氣較冷,空氣濕度較高;漆膜干燥后,受到寒冷、雨露、煙霧、酸、堿或潮氣的浸蝕;
(4)基材表面處理不當,被涂物表面殘留有酸、堿、鹽、油污等沒有徹底清除干凈時涂裝底漆,或在底漆未干透時涂裝面漆,造成局部慢干或發(fā)粘;
(5)施工時,雙組份涂料固化劑沒有添加或添加量不夠,烘干型涂料烘干不足,或需空氣氧化的涂料施工場所潮濕而不通風等。
改善對策
(1)采用揮發(fā)適中的稀釋劑,對于慢干型涂料,可適當采用揮發(fā)較快的溶劑;
(2)調整催干劑的用量;
(3)施工時,注意環(huán)境溫度不能太低,當氣溫低于10℃時,應采用冬季固化型涂料或單組份溶劑揮發(fā)型涂料;涂裝完成后,漆膜需經約2個星期的保養(yǎng)時間方可在腐蝕介質中使用;
(4)涂漆前應將底材進行良好的表面處理,漆膜不能涂裝過厚,底漆和其它涂層一定要實干后,再涂裝下一道涂料;嚴格按照產品說明書的要求進行施工,防止底漆中的溶劑未完全揮發(fā)帶來的發(fā)粘現(xiàn)象;
(5)施工時,對于雙組份涂料應嚴格按要求進行漆與固化劑的配比,同時應有一定的熟化時間;烘干型涂料應選擇適宜的烘干溫度,增加施工場所的通風性,避免潮濕環(huán)境;
成因
(1)在高濕度、通風、工業(yè)煙氣、廚房氣體等環(huán)境中,漆膜易起霜;
(2)烘漆中,施工時溫度變化幅度過大,或室內涂裝時空氣流通量不足;
(3)催干劑選用不當,增塑劑遷移至表面。
改善對策
(1)排除方法:用柔軟的抹布沾溫熱水,擰干水份后將漆膜表面擦拭一遍;用干抹布揩凈水的印跡,直到漆膜呈現(xiàn)出原來的光亮度為止;為避免重復起霜,可在擦拭后的漆膜表面涂一層憎水劑;
(2)對烘干漆應先放置一段時間,再進行烘烤;
(3)選用合適的催干劑。
成因
(1)底層涂料干燥后,表面沾有油脂性、水及鐵銹等物質,涂后道涂料時又沒有很好進行處理;
(2)底層涂料固化成膜后,在其上復涂一層時,該底層涂膜未進行打毛處理,或打毛工作進行得粗糙;
(3)底漆暴露時間過長,干得太透、太堅硬或有較高光澤。
改善對策
(1)對已干燥固化成膜的漆膜,必須進行打毛成粗糙涂面,同時必須保持涂面潔凈;
(2)為提高面漆與底漆間的層間附著力,底漆應經打磨后施工面漆,且第一道面漆宜薄涂,表干后再涂第二道面漆;第一道面漆采用薄涂,此后再結合“濕碰濕”的施工方法,涂第二道、三道面漆;
(3)底漆固化后應及時進行下一道涂裝。
成因
(1)金屬表面處理較差,有鐵銹、機油等污物;
(2)底材潮濕或未完全干透,涂漆后溶劑或水氣揮發(fā)時向外擴散,頂起漆膜而起泡;
(3)空氣壓縮機及管道中常帶有水份,使面漆起泡;
(4)在多孔表面涂裝時,沒有將孔眼填實,在干燥過程中孔眼中的空氣受熱膨脹形成氣泡;
(5)在強烈的日光下或高溫下涂裝,涂層厚度過高,表層涂料雖經日曬干燥,但熱量傳入內層涂料后,涂層中的溶劑迅速揮發(fā),造成漆膜起泡;
(6)烘烤型涂料急劇加熱,漆膜易起泡。
改善對策
(1)工件施工前應徹底除油、除銹,并做到表面干燥;
(2)底材、膩子必須干透,方可進行下道漆的施工;
(3)檢查油水分離器,并清除噴涂設備中的凝結水;
(4)在多孔的表面上,應先涂一層稀薄的漆液,使封閉的空氣及時逸出;
(5)避免在強烈的日光下或高溫下涂裝,且涂層厚度應合適;
(6)烘烤型油漆在涂漆后應在室溫下靜置一段時間,烘烤時先低溫預熱,再按規(guī)定進行烘烤;漆膜如有氣泡,則應視情況決定是局部修補還是脫除后重新涂漆。
成因
(1)空氣相對濕度過大(一般大于80%時),或涂料中揮發(fā)性溶劑的含量過高,噴涂的揮發(fā)性漆中的溶劑揮發(fā),使漆膜表面溫度降低,水份向漆膜上凝結造成泛白或噴涂設備中有大量水份凝結,噴涂時水份被帶入漆中,也常常造成漆膜泛白。
改善對策
(1)嚴格控制施工環(huán)境的溫濕度,尤其是控制環(huán)境的相對濕度不大于70%;在濕度大的條件下施工時應采取工件低溫預熱或加入適量防潮劑的方法;對于設備中的水份,應徹底清除,并檢查油水分離器的可靠性;在低沸點稀料內添加防潮劑,稀料內有水份時應予以更換。
成因
(1)施工時,環(huán)境濕度過大;
(2)底層多孔,且對面漆具有很強的吸附力,使面層涂料有很好的滲透作用,面層涂料滲入底層,光澤下降;
(3)底層涂層不潔凈,漆膜上的油污、水跡未清除干凈;
(4)顏料和溶劑內含水較多,制漆后均勻分布于漆液中,這些水份不僅會產生針孔、起泡,且會引起失光;
(5)施工時稀料使用不當或用量過多,也會造成漆膜光澤下降;
(6)面漆漆膜過薄,涂裝面不平整。
改善對策
(1)嚴格控制施工環(huán)境和施工條件,避免在陰冷潮濕的環(huán)境中施工;
(2)對底層進行適當處理;
(3)將底漆表面清除干凈之后再噴涂面漆;
(4)檢查顏料和溶劑內含水量并采取措施;
(5)采用專用稀釋劑并使用合適比例;
(6)漆膜失光,應在漆膜實干后,重新涂裝。
成因
(1)施工工具、稀釋劑中含有微量水,或由羥基組份中帶來,微量水與漆液中-NCO基起反應,放出CO2,加上表干較快,使CO2無法逸離漆膜;或施工工件表面孔隙中有水汽;
(2)涂料中低沸點溶劑太多,特別在35℃以上施工,或由于噴涂較厚,進入烘箱過快,或烘烤溫度過高,溶劑散逸不出來而形成小泡。
(3)施工時粘度過大,配漆時混入的空氣沒有散逸就進行施工,微氣泡在漆膜表干前沒有散離出去;
(4)施工后的工件在常態(tài)下沒有放置或放置的時間較短,就放入烘箱烘烤;或雖放置了足夠時間,但烘烤溫度過高,表干加快,溶劑散逸不出來而造成氣泡;
(5)噴涂壓力過大,距離過遠,破壞了濕漆膜的溶劑平衡,也易產生針孔;
(6)施工濕度過高,噴涂設備油水分離器失靈,空氣未過濾,噴涂時水氣隨空氣管帶入噴出,引起漆膜表面的針孔,甚至是水泡;
(7)被涂物表面處理不當,在有油污的表面上涂裝。
改善對策
(1)嚴禁水份進入漆料中,施工工件表面多孔隙,在濕熱、陰雨時應烘干后施工;
(2)適量增加高沸點溶劑的用量;
(3)調整施工粘度;
(4)施工后的工件,在常態(tài)下放置0.5h左右,烘烤時溫度控制在50-60℃為宜,且最好從室溫下升至50-60℃;
(5)嚴格控制施工粘度、噴涂壓力,也有利于減少針孔。
(6)控制好施工濕度,保證噴涂設備油水分離器有效;
(7)底材處理應無油且除塵后須達到一定的表面處理等級;對于已經形成針孔的漆膜表面,可補涂配套涂料;表面不平整時,磨平后再涂裝。
成因
(1)工件表面或噴涂器具系統(tǒng)有油污或水汽微珠;
(2)底材或底漆太光亮,聚氨酯樹脂涂料難以附著;
(3)雙組份漆在配漆后,沒有放置熟化使其預聚合,立即施工時,也易產生麻坑;
(4)噴涂的粘度過大,施工環(huán)境溫度過低,漆膜難流平,輕者為橘皮,重者為凹坑;另施工時噴涂壓力過大,重者也形成凹坑;
(5)噴涂時漆液中有大量氣泡,成膜后氣泡破裂,形成麻坑。
改善對策
(1)確保施工工件表面或噴涂器具系統(tǒng)無油污、無水珠;
(2)對施工工件表面進行適當?shù)奶幚恚?br />
(3)雙組份漆配制后,按產品要求進行充分熟化(放置)后,再施工;
(4)嚴格控制施工工藝條件(施工粘度14-18s,噴槍壓力(0.3-0.4)×105Pa、排風速度(0.2-0.4m/s)、噴槍與工件距離(20-30cm));
(5)加入適量的流平劑和其它助劑。
成因
(1)油漆配方未調至最佳;
(2)施工時粘度過大,涂料舒展流平慢;噴槍口徑太小,與工件距離不適合,造成漆霧粒子大,影響了漆的流平;噴涂壓力過大,高氣壓粒子撞擊,造成漆膜不平整;
(3)溶劑揮發(fā)速度快,過度通風,被涂物的溫度高等,妨礙涂料流平;
(4)施工溫度過高或過低,都會影響涂料的流平;溫度過高,溶劑揮發(fā)過快,不利于流平;過低,液態(tài)漆膜內漆料呈高粘度,也不利于流平;
(5)過早地進入高溫烘箱內烘干;
(6)被涂物面不光滑,影響涂料的流平或對涂料的吸收。
改善對策
(1)加入適量流平劑或調整配方;
(2)控制適當?shù)氖┕ふ扯龋?4-18s),噴槍壓力(0.3-0.4)×105Pa、排風速度(0.2-0.4m/s)、噴槍與工件距離(20-30cm)等可控條件;
(3)增大稀釋劑中高沸點溶劑的比例;控制適宜的施工環(huán)境溫度(20-30℃)與通風條件,被涂物溫度應在50℃以下;
(4)控制好施工溫度;
(5)注意施工技巧,正確施工,控制漆膜厚度,保證足夠的干燥時間和流平;烘干型漆膜應放置一段時間后,由低溫至高溫,按規(guī)定烘干;
(6)底材應經嚴格處理,但粗糙度不宜過大;對吸收性強的底層應先涂一層底漆,使其平整光滑;對出現(xiàn)橘皮的漆膜,需用細砂紙將 痕跡磨平,除去灰塵后再噴涂一道面漆。
成因
(1)底層涂料采用氣干性的底漆(如硝基底漆、丙烯酸酯改性硝基底漆),或采用了不耐溶劑的底漆(如鐵紅酚醛底漆、紅灰酚醛底漆等),當在其上與聚氨酯漆配套時,聚氨酯漆的強溶劑滲透到底層漆膜中,使該底漆漆膜發(fā)生軟化、溶脹、鼓起;
(2)底漆雖采用了聚氨底漆、環(huán)氧樹脂底漆等耐溶劑性優(yōu)的底漆,但底漆并未干透就在其上施工聚氨酯面漆,面漆中的強溶劑滲透到未干透的漆膜中,造成底漆涂層局部產生溶脹、軟化出現(xiàn)咬底;
(3)漆膜涂裝時涂得過厚,未能完全干透。
改善對策
(1)對于氣干性不耐強溶劑的底漆,在其上噴涂含強溶劑的面漆時, 第一道一定要薄涂,表干后,再施工第二、三道面漆;
(2)涂料應完全干透,按照最佳時間間隔執(zhí)行,必須達到最短涂裝間隔;
(3)對于發(fā)生“咬底”的涂料,不能再起到保護和裝飾的作用,應鏟 去咬底部位的漆膜,補涂并改進配套。
成因
(1)漆料太稀,施工道數(shù)太多,濕漆膜太厚;
(2)涂料干燥固化較快,而涂料中的溶劑揮發(fā)的又太慢;
(3)施工環(huán)境溫度太低,不利于涂料的干燥固化和溶劑的揮發(fā);
(4)噴涂時噴嘴口徑太大,噴槍壓力不均勻,噴槍與施工工件距離太近, 噴涂施工時走槍速度太慢;
(5)施工方式不當,被涂物件表面凸凹不平,幾何形狀復雜;
改善對策
(1)控制適宜的施工粘度,最好在14-18s之間(夏季可適當偏低些14-16s,冬季可適當偏高些16-18s);
(2)調整涂料中的溶劑揮發(fā)速度;
(3)盡可能使施工環(huán)境溫度控制在20-30℃的范圍內;
(4)控制適宜的走槍速度,一般不要低于20cm/s;噴槍與工件距離在20-30cm范圍,噴槍壓力控制在(0.3-0.4)×105Pa為宜;
(5)改變施工方式。
成因
(1)粉末混人粗粒狀異物
(2)粉末在噴嘴處黏附硬化
(3)輸送粉時氣壓過低
改善對策
(1)將粉末過篩
(2噴嘴經常清洗
(3)加大輸粉氣壓
成因
(1)噴室回收袋不吸塵
(2)抽風管堵塞
(3)氣壓太高,出粉量多
改善對策
(1)檢查回收袋
(2)檢查抽風管
(3)調整氣壓
在線咨詢
請?zhí)岢瞿膯栴},我們會盡快給您回復!